Home - Search - Browse - Alphabetic Index: 0- 1- 2- 3- 4- 5- 6- 7- 8- 9
A- B- C- D- E- F- G- H- I- J- K- L- M- N- O- P- Q- R- S- T- U- V- W- X- Y- Z
Magnum HLLV
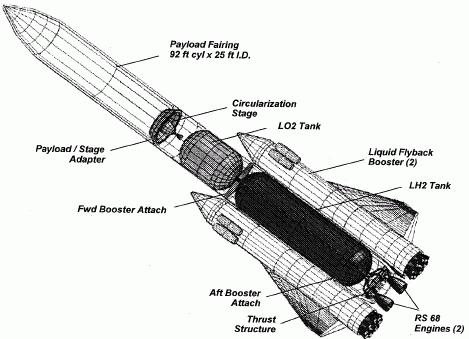
Magnum
Credit: NASA
American heavy-lift orbital launch vehicle. Notional NASA/MSFC heavy lift booster design, using no shuttle components but instead new technologies from the EELV and RLV programs that supposedly would reduce launch cost by a large factor. A composite core vehicle powered by RS-68 engines was flanked by two shuttle liquid rocket boosters. Baseline launch vehicle used in most NASA manned lunar and Mars mission studies 1996-2004.
AKA: Magnum. Status: Study 1996. Payload: 80,000 kg (176,000 lb). Thrust: 30,000.00 kN (6,744,000 lbf). Gross mass: 2,130,000 kg (4,690,000 lb). Height: 98.17 m (322.08 ft). Diameter: 8.40 m (27.50 ft). Apogee: 407 km (252 mi).
Human Mars mission launch costs were driven by initial mass in low-Earth-orbit (IMLEO); launch costs per kilogram of payload; launch vehicle development costs; and on-orbit assembly costs. Earth-to-Orbit (ETO) metrics identified in DRM 3.0 required launch vehicle payload capability of 80 metric tons to minimize on orbit assembly costs and meet payload size requirements. Cost metrics of less than $2200 launch cost per kilogram of payload and total mission costs of $6 billion for any launch vehicle development costs and all launch recurring costs were designated as reasonable starting requirements to drive system designs.
During the design cycle for Reference Mission Version 1.0 numerous configurations were considered and a Shuttle derived vehicle (SDV) with an inline core vehicle was selected. The SDV launch concept barely meets the $6B cost metric for total mission ETO costs because of the high core vehicle costs for Shuttle common hardware. In addition, recent analysis indicated that the SDV configuration exceeded the $2200/kg metric by a factor of two.
Launch vehicle assessments for Reference Mission 3.0 focused on evaluating a core vehicle that was not Shuttle derived to decrease launch costs. Advances in launch vehicle technologies from the Reusable Launch Vehicle (RLV) and Evolved Expendable Launch Vehicle (EELV) programs could make it cost effective to develop a core vehicle that would potentially reduce the $6B ETO cost metric to $2.5B or less per current estimates. This new vehicle concept was designated "Magnum" to differentiate it from the numerous other previous launch vehicle studies. The Magnum configuration was an inline core vehicle with two attached Shuttle boosters. The payload was aft mounted on the expendable core vehicle, similar in configuration to the Titan IV but with over five times the payload capability for one third the launch cost.
The Magnum vehicle configuration includes a core component which was 8.4 meters in diameter, the same as the Shuttle External Tank, to allow common use of Shuttle boosters and launch facilities. By using Shuttle launch facilities and the proposed Liquid Fly Back Boosters (LFBB), recurring costs was estimated to be less than $2200 per kilogram of payload. A composite shroud was used to protect the payload during ascent and a small kick stage was used for circularizing the orbit. The design of the Magnum launch vehicle provided a delivery capability of 85 metric tons to 407 km orbits at 28.5 degrees inclination or 80 metric tons to 51.6 degree inclination orbits. Payloads with diameters of up to 7.5 m and lengths of 27.7 m could be accommodated.
Technology development and demonstrations for the Magnum launch vehicle concept were driven by the large vehicle size and low life cycle cost requirements. Evaluations were focused on maximizing the cost-effective application of technologies for engines, valves, composite tanks/structures, and other hardware or facilities then under development or projected to be available on other programs such as RLV or EELV. The proposed Magnum technology development program would physically extend these technologies to fit Magnum. Tasks would need to be conducted to demonstrate 8.8 meter diameter composite fuel tank manufacturing techniques derived from techniques developed on substantially smaller tanks for RLV.
Equivalent tasks would be conducted to demonstrate large composite shrouds using the Advanced Grid Stiffened (AGS) composite shroud manufacturing techniques first developed for EELV by the USAF Phillips Lab. Composite structures, propellant ducts and valve technologies would also need to be demonstrated. Though the Magnum configuration using LFBBs was selected to drive technology developments, the Magnum configuration was still open for assessment of alternate boosters, engines, etc. which would meet requirements.
Boeing sketched out several variants for Magnum, using different strap-on booster concepts, but with a common core design:
- MLV-SDV-1a: 2 RSRB's; ET diameter core with 1.5 m stretch; 2 low pressure / low cost engines with 295 metric tons thrust and 416s specific impulse; kick stage for circularization; shroud with 7.6 m x 28 m capacity. 2095 metric tons gross lift-off mass; 55 metric tons payload to a 407 x 407 km orbit at 28.5 deg . DDT&E cost: $1.46 billion; first unit cost: $ 279 million; average unit cost (over 25 flights): $ 230 million = $ 4227/kg.
- MLV-SDV-1b: 4 RSRB's; ET diameter core with 1.5 m stretch; 2 low pressure / low cost engines with 295 metric tons thrust and 416s specific impulse; core air start at T+100 seconds; kick stage for circularization; shroud with 7.6 m x 28 m capacity. 3329 metric tons gross lift-off mass; 94 metric tons payload to a 407 x 407 km orbit at 28.5 deg . DDT&E cost: $1.46 billion; first unit cost: $ 359 million; average unit cost (over 25 flights): $ 308 million = $ 3280/kg.
- MLV-SDV-2: 2 RSRB's; ET diameter core with 1.5 m stretch; 2 P/A modules; 2 SSME per P/A module; kick stage for circularization; shroud with 7.6 m x 28 m capacity. 2130 metric tons gross lift-off mass; 80 metric tons payload to a 407 x 407 km orbit at 28.5 deg . DDT&E cost: $2.26 billion; first unit cost: $ 294 million; average unit cost (over 25 flights): $ 237 million = $ 2970/kg.
- MLV-SDV-3: 2 pump fed LRB's; ET diameter core with 1.5 m stretch; 2 low pressure / low cost engines with 295 metric tons thrust and 416s Isp; 3 RD-180 lox/kerosene engines per LRB; kick stage for circularization; shroud with 7.6 m x 28 m capacity. 2367 metric tons gross lift-off mass; 91 metric tons payload to a 407 x 407 km orbit at 28.5 deg . DDT&E cost: $2.00 billion; first unit cost: $ 494 million; average unit cost (over 25 flights): $ 354 million = $ 3883/kg.
- MLV-SDV-4: 2 pressure fed LRB's; ET diameter core with 1.5 m stretch; 2 low pressure / low cost engines with 295 metric tons thrust and 416s Isp; 4 x 360 metric ton thrust lox/kerosene pressure-fed engines per LRB; kick stage for circularization; shroud with 7.6 m x 28 m capacity. 3224 metric tons gross lift-off mass; 64 metric tons payload to a 407 x 407 km orbit at 28.5 deg . DDT&E cost: $2.41 billion; first unit cost: $ 669 million; average unit cost (over 25 flights): $ 501 million = $ 7834/kg
- MLV with LFBB: Concept Description: 2 liquid flyback boosters; ET diameter core, no stretch; 2 low pressure / low cost engines with 295 metric tons thrust and 416s specific impulse; RD-180 Lox / kerosene booster engines, 680 metric tons thrust each with 338s specific impulse; kick stage for circularization; shroud with 7.6 m x 28 m capacity. 2594 metric tons gross lift-off mass; 93 metric tons payload to a 407 x 407 km orbit at 28.5 deg . DDT&E cost: $1.46 billion (excludes LFBB cost, assumed to have already been developed for shuttle program); first unit cost: $ 225 million; average unit cost (over 25 flights): $ 174 million = $ 1872/kg
Only the last option came close to meeting NASA's requirement for a development cost under $ 1.9 billion and a cost per kilogram in orbit of under $2194. But this assumed development of reusable liquid flyback boosters for the shuttle program, which did not occur. NASA estimated the LFBB would take $ 4.0 to $ 5.0 billion to develop, making the last option uneconomical for the low number of launches anticipated. This would then make the shuttle-derived MLS-SDV-2 the most economical option, and that is the vehicle for which the detailed breakdown of performance is provided.
LEO Payload: 80,000 kg (176,000 lb) to a 407 km orbit at 28.50 degrees. Development Cost $: 2,260.000 million. Launch Price $: 237.000 million in 1997 dollars in 1997 dollars.
Stage Data - Magnum
- Stage 0. 2 x Shuttle RSRM. Gross Mass: 590,000 kg (1,300,000 lb). Empty Mass: 88,000 kg (194,000 lb). Thrust (vac): 11,519.999 kN (2,589,799 lbf). Isp: 267 sec. Burn time: 123 sec. Isp(sl): 235 sec. Diameter: 3.77 m (12.36 ft). Span: 5.10 m (16.70 ft). Length: 45.46 m (149.14 ft). Propellants: Solid. No Engines: 1. Engine: RSRM. Other designations: Redesigned Solid Rocket Motor. Status: In production. Comments: After the Challenger disaster the redesigned solid rocket motors had a slight reduction in performance due to reliability improvements.
- Stage 1. 1 x Magnum Core. Gross Mass: 830,000 kg (1,820,000 lb). Empty Mass: 70,000 kg (154,000 lb). Thrust (vac): 9,112.378 kN (2,048,544 lbf). Isp: 453 sec. Burn time: 500 sec. Isp(sl): 363 sec. Diameter: 8.40 m (27.50 ft). Span: 8.40 m (27.50 ft). Length: 53.00 m (173.00 ft). Propellants: Lox/LH2. No Engines: 4. Engine: SSME. Status: Conceptual design, 1998. Comments: Alternative configurations used 2 to 3 RS-68 engines.
Family:
heavy-lift,
orbital launch vehicle.
Country:
USA.
Stages:
Magnum Core,
RSRM.
Agency:
NASA Houston.
Back to top of page
Home - Search - Browse - Alphabetic Index: 0- 1- 2- 3- 4- 5- 6- 7- 8- 9
A- B- C- D- E- F- G- H- I- J- K- L- M- N- O- P- Q- R- S- T- U- V- W- X- Y- Z
© 1997-2019 Mark Wade - Contact
© / Conditions for Use